Mario Juez-Gil1, Juan José Saucedo-Dorantes2
, Álvar Arnaiz-González1
, Carlos López-Nozal1
and César García-Osorio1
1 Departamento de Ingeniería Informática, Universidad de Burgos, 09006 Burgos, Spain
2 Engineering Faculty, Autonomous University of Querétaro, San Juan del Rio 76806, Mexico
Keywords: Multi-fault detection, Early detection, Predictive maintenance, Multi-label classification, Principal component analysis, Industry 4.0.
1. Introduction
This extended abstract highlights the main contributions of the paper [1], previously published in ISA Transactions. The publication presented an intelligent framework for diagnosing single, or multiple malfunctions occurring in Induction Motors (IM) using only the measurements recorded during the initial milliseconds of operation. Many industrial applications involve the use of IM, which represent the most used electrical machines. This is due to their robustness, efficiency, and safety. Unexpected faults in this kind of machinery, could provoke undesirable interruptions that may lead to crucial interruptions in industrial processes. Continuous monitoring, by means of registering data acquired from different kind of sensors, can play a fundamental role to ensure the machinery reliability and safety in industrial production systems [2, 3].
The use of Artificial Intelligence (AI) and classification techniques have been included as a part of the condition monitoring strategies. These techniques usually consist of several steps: data collection (gathering fault-related measurements); feature calculation, extraction, and selection (determining fault-related features and measurements); and, training an algorithm (building a classification model with the selected features) [4, 5, 6]. A trained AI model will be capable of identifying the relationship between both input data (information provided by sensors) and output data (machine-assessed condition), which is of great value in assisting or even replacing human intervention. Depending on the format of the output data, the problem to be solved will be one or another. When there is a single output (i.e., label) representing the faulty condition, the problem is referred to as single-label classification. However, more than one label can be assigned whenever multiple faults occur simultaneously. This task, known as multi-label classification, has been the focus of recent research [7, 8].
2. Multi-fault early diagnosis method
2.1- Data set description
The data set was built using the measurements obtained in an experimental test bench. It contains three types of faulty condition: broken rotor bar (BRB), unbalance (UNB), and misalignment (MAL). Those faults may occur isolated, or at the same time. If the IM is working properly, we say that it presents a healthy (HLT) condition. Thus, in the data set used, the different combinations of the three operating faults considered give rise to 8 different operating conditions. The data set contains examples of motors operating at low, medium, or high frequencies: 3 Hz, 30 Hz, and 60 Hz (direct supply), respectively. Those examples were obtained from motors operating at three different load capacities: unloaded, half load, and full load. The first 5 seconds of the IM start-up were registered using sensors. The measurements taken were: currents (current A, curr. B, curr. C, and curr. N), voltages (voltage A, volt. B, and volt. C), the rotational speed, and vibrations (accelerometer X, acc. Y, acc. Z, and an acc. reference). As there were eight measures sampled at 12 kHz, and four measures sampled at 3 kHz, a single instance consisted in 540,000 attributes. The data set contains a total of 2,521 instances.
2.2- Proposed method
Our method is a two-step approach. Firstly, the number of attributes is dramatically reduced from 540,000 to only 139, by means of PCA. A thorough study of the optimal number of principal components to retain for each type of sensor using K1 rule, Scree test [9] and hyperparameter optimization [10], was performed. Fig. 1 shows how PCA was applied to each of the sensors. Secondly, the reduced data is passed to a multi-label decision tree classifier that will decide what the operating condition of the IM is. More specifically, the classifier output will be the presence or absence of each of all three possible faulty conditions (UNB, MAL, and BRB).
3. Results
For evaluating the results, six multi-label metrics were used: F1 macro, F1 micro, accuracy, ranking loss, Hamming loss, and zero-one loss. A study was carried out on the minimum number of measurements needed to obtain accurate predictions (i.e., the earliest possible fault detection). For all the metrics, using only the first 0.5 seconds of operation, resulted in statistically equivalent results to those obtained using all measurements (i.e., 5 seconds). For that narrow time window, multi-label decision trees provided fault detection accuracies over 90%: 91.1% at 3 Hz, 94.5% at 30 Hz, and 90.2% for direct supply. Although the operation frequency is commonly known, models trained with data from all the frequencies (i.e., frequency-insensitive model) also showed to be feasible and accurate enough (87.6%), which undoubtably is an additional strength of this proposal. Fig. 2 shows the confusion matrices for the four predictive models, it can be seen the high accuracy for all faulty conditions, and which faults are most susceptible to be misclassified.
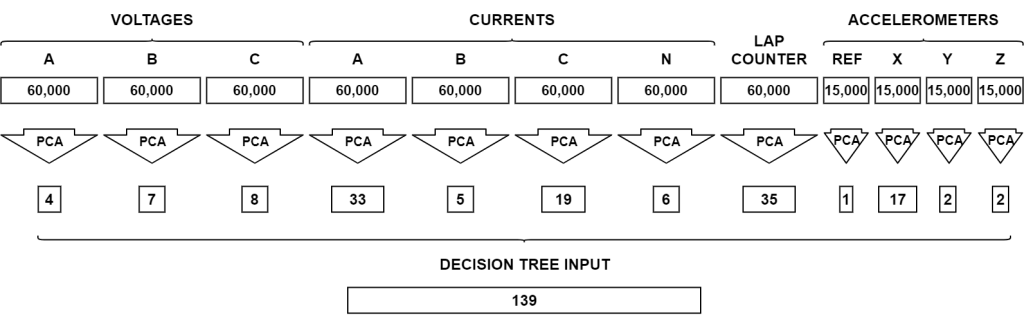
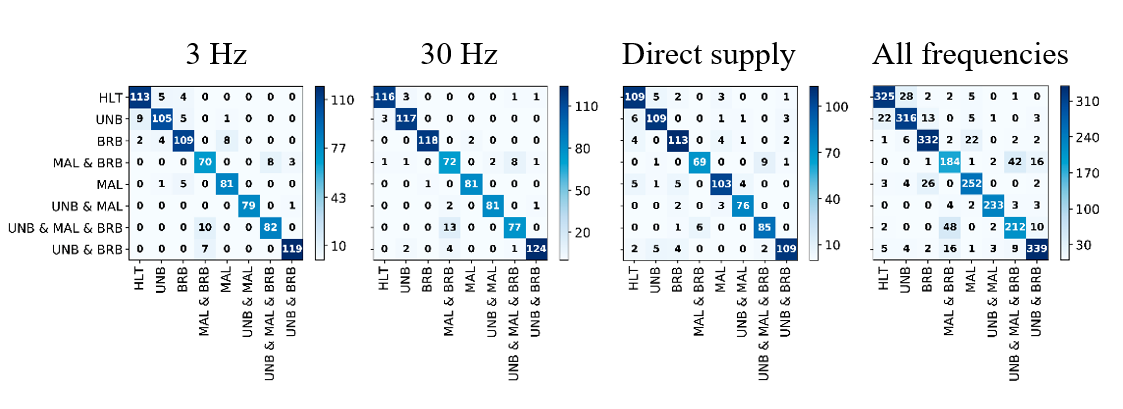
4. Conclusions
In this work, a new technique based on multiple sensor information for early diagnosis (only the first 0.5 seconds of measures are needed) of single, combined, and simultaneous faulty conditions in IM has been proposed and validated. This problem has normally been addressed by using signal processing based on time domain, frequency domain, and time-frequency domain analyses. However, those techniques have shown some shortcomings, for example, at fault prediction on low operational frequencies.
Our method is capable of accurately predicting faults for any frequency. It was validated on motors operating at low, medium, and high frequencies. Moreover, a frequency-insensitive method can be trained using examples from all frequencies. Our method demonstrated to also be insensitive to the mechanical load of the motor, which, for some other approaches, may be a critical factor affecting its performance.
Our intuition was that thanks to the application of PCA, the most representative fault-related information was extracted, which was essential for building high-performing multi-label decision trees. Without PCA, the use of expert knowledge about each specific type of failure would have been essential.
References
- Juez-Gil, M., Saucedo-Dorantes, J. J., Arnaiz-González, Á., López-Nozal, C., García-Osorio, C., & Lowe, D. (2020). Early and extremely early multi-label fault diagnosis in induction motors. ISA transactions, 106, 367-381.
- Liu, Y., & Bazzi, A. M. (2017). A review and comparison of fault detection and diagnosis methods for squirrel-cage induction motors: State of the art. ISA transactions, 70, 400-409.
- Liu, R., Yang, B., Zio, E., & Chen, X. (2018). Artificial intelligence for fault diagnosis of rotating machinery: A review. Mechanical Systems and Signal Processing, 108, 33-47.
- Martin-Diaz, I., Morinigo-Sotelo, D., Duque-Perez, O., Osornio-Rios, R. A., & Romero-Troncoso, R. J. (2018). Hybrid algorithmic approach oriented to incipient rotor fault diagnosis on induction motors. ISA transactions, 80, 427-438.
- Lei, Y., Jia, F., Lin, J., Xing, S., & Ding, S. X. (2016). An intelligent fault diagnosis method using unsupervised feature learning towards mechanical big data. IEEE Transactions on Industrial Electronics, 63(5), 3137-3147.
- Saucedo-Dorantes, J. J., Delgado-Prieto, M., Osornio-Rios, R. A., & de Jesus Romero-Troncoso, R. (2016). Multifault diagnosis method applied to an electric machine based on high-dimensional feature reduction. IEEE Transactions on industry applications, 53(3), 3086-3097.
- Tsoumakas, G., & Katakis, I. (2007). Multi-label classification: An overview. International Journal of Data Warehousing and Mining (IJDWM), 3(3), 1-13.
- Zhang, M. L., & Zhou, Z. H. (2013). A review on multi-label learning algorithms. IEEE transactions on knowledge and data engineering, 26(8), 1819-1837.
- Zwick, W. R., & Velicer, W. F. (1986). Comparison of five rules for determining the number of components to retain. Psychological bulletin, 99(3), 432.
- Bergstra, J., Bardenet, R., Bengio, Y., & Kégl, B. (2011, December). Algorithms for hyper-parameter optimization. In 25th annual conference on neural information processing systems (NIPS 2011)(Vol. 24). Neural Information Processing Systems Foundation.