Juan De Antón1, David J. Poza1
, Adolfo López-Paredes1
and Félix Villafáñez1
1 INSISOC – University of Valladolid. Paseo del Cauce 59, 47011 Valladolid, Spain
Keywords: Production Planning, Additive Manufacturing, 3D printing, Nesting, Scheduling.
1. Introduction
Contrary to traditional manufacturing, additive manufacturing (AM) offers desirable features for customized sustainable production. However, whereas topics on production planning in traditional manufacturing have been extensively studied, issues regarding operations management (OM) in AM-based production systems have not been completely addressed. This is especially noticeable for planning and scheduling problems [1].
As AM continues its journey to maturity as a production technique, the focus has been set on reaching mass production of customized products [2]. Reaching mass production entails the manufacture of large quantities of heterogeneous parts, which involves a variety of subproblems such as manufacturing multiple parts in the same batch or scheduling one machine to produce several batches [3]. In the AM field, these two problems are known as nesting problem and scheduling problem, respectively. We claim that, when merging both nesting and scheduling problems, it is common to fall into vague definitions of the subproblems included in each concept.
2. Literature Review
The research literature on production problems in AM has evolved significantly over time. In the beginning, the nesting problem was defined for AM production contexts and the first models seeking its optimization were developed [4]. Later, the nesting problem was extended by including scheduling questions [2]. More recently, nesting and scheduling have been addressed together, which result in more complex and comprehensive models.
Although there already exist reviews on AM production planning [5,6], their proposals still consider only parts of the whole range of production planning problems. At the same time, these works fall short in providing researchers and practitioners with a robust framework for identifying the wide variety of subproblems enclosed in nesting and scheduling.
In this context, the aim of this paper is to propose a framework that includes a clear definition of the specific problems faced by production planning in AM.
3. Framework for Production Planning in Additive Manufacturing
The framework that we propose describes the sequence followed by the manufacturer when he or she addresses the production planning of the 3D factory. Figure 1 shows this sequence in the two-stage planning procedure.
The procedure starts with the reception of several part orders from distributed customers. Then, these parts, whether grouped or not, must be assigned to a suitable AM machine (i.e. 3D printer). These steps comprise the first stage, which is the Part/Machine assignment (figure 1, left). Hence, the allocation and placement of parts in each machine are solved by creating batches in the nesting step. Finally, the sequence for processing all those batches and their production start-up times are determined. These activities belong to the second stage: Machine scheduling (figure 1, right).
In our framework, each problem is thoroughly defined, and their inputs, outputs and objectives are indicated.
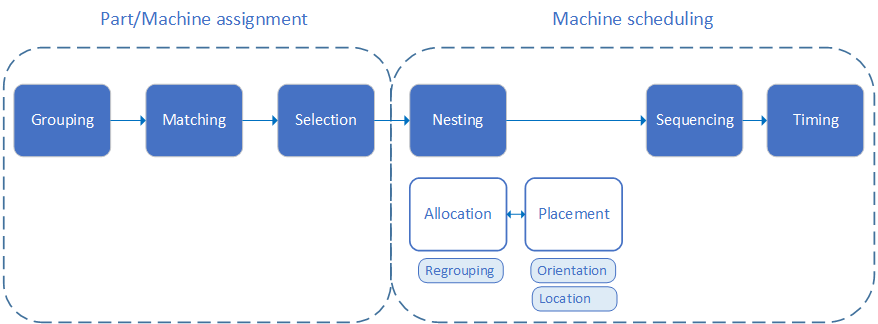
4. Conclusions
In this paper, we have provided a framework for production planning in additive manufacturing (AM). This framework aims to bring clarity to the myriad of production problems that have emerged as AM production planning advances towards its maturity.
We are hopeful that the proposed framework provides a helpful tool for researchers and practitioners to better understand the planning process in AM. It also opens the opportunity to use this framework as the basis for a systematic review and categorization of the heterogeneous models for nesting and scheduling proposed in the literature. It will allow pinpointing the best solutions developed so far for the optimization of production planning in AM.
References
- Manco, P. et al. (2019) ‘The additive manufacturing operations management maturity: A closed or an open issue?’, Procedia Manufacturing, 41, pp. 98–105. doi: 10.1016/j.promfg.2019.07.034.
- Oh, Y. et al. (2020) ‘Nesting and scheduling problems for additive manufacturing: A taxonomy and review’, Additive Manufacturing, 36(August), p. 101492. doi: 10.1016/j.addma.2020.101492.
- Kucukkoc, I. (2019) ‘MILP models to minimise makespan in additive manufacturing machine scheduling problems’, Computers and Operations Research, 105, pp. 58–67. doi: 10.1016/j.cor.2019.01.006.
- Zhang, Y., Gupta, R. K. and Bernard, A. (2016) ‘Two-dimensional placement optimization for multi-parts production in additive manufacturing’, Robotics and Computer-Integrated Manufacturing, 38, pp. 102–117. doi: 10.1016/j.rcim.2015.11.003.
- Araújo, L. J. P. et al. (2018) ‘Analysis of irregular three-dimensional packing problems in additive manufacturing: a new taxonomy and dataset’, International Journal of Production Research, 57(18), pp. 5920–5934. doi: 10.1080/00207543.2018.1534016.
- Oh, Y., Zhou, C. and Behdad, S. (2018) ‘Production planning for mass customization in additive manufacturing: Build orientation determination, 2D packing and scheduling’, Proceedings of the ASME Design Engineering Technical Conference, 2A-2018(August). doi: 10.1115/DETC2018-85639.